Monitoraggio del circuito di raffreddamento nei serbatoi di fermentazione della distilleria
Distilleria Steinhauser
Sapere quanta energia viene utilizzata nella produzione di liquori e vini
Nel processo di produzione di vini e liquori, l’attenzione è concentrata sul processo di fermentazione, durante il quale la temperatura deve essere costantemente monitorata per garantire il gusto, il sapore e la qualità ottimale dei prodotti. Se il processo di fermentazione viene rallentato o interrotto, il prodotto si raffredda nel serbatoio. Anche una piccola deviazione nel tempo di fermentazione può comportare una significativa perdita di aroma.
La temperatura viene regolata da Steinhauser Hausbrennerei & Weinkellerei con due grandi unità di refrigerazione. La loro rete di linee di raffreddamento è collegata a ogni serbatoio della produzione. Il liquido di raffreddamento nelle linee di alimentazione e di scarico viene monitorato mediante sensori.
Situazione iniziale
Negli ultimi anni l’azienda Steinhauser è cresciuta ulteriormente tanto che la capacità richiesta dell’unità di raffreddamento non era più garantita. Inoltre, non era possibile acquisire dati sui costi energetici per la produzione di un prodotto.
Obiettivo del progetto
Misurazione dell’energia nel processo di produzione degli alcolici
È necessario garantire che la quantità di refrigerante richiesta sia rapidamente disponibile nel serbatoio corrispondente. Il collegamento a moneo consentirà per la prima volta di monitorare e documentare l’energia di raffreddamento effettivamente utilizzata. Così si potranno trarre conclusioni sulle quantità di energia consumata per la produzione.
Realizzazione
Sono stati acquistati due nuovi sistemi di refrigerazione nell’area esterna dell’azienda Steinhauser. In seguito è stata eseguita l’installazione della tubazione per ogni singolo serbatoio di fermentazione. I sensori di flusso e di temperatura sono stati installati nelle condotte di mandata e ritorno di ciascuna linea dell’acqua di raffreddamento. I dati di processo vengono trasmessi al sistema moneo, installato su moneo|appliance, tramite master IO-Link. Con moneo RTM, tutti i valori di processo delle condotte di mandata e ritorno delle rispettive linee di produzione vengono registrati e visualizzati.
La funzione Data Flow Modeler in moneo si possono creare "valori calcolati" per calcolare la capacità di raffreddamento attuale. Inoltre, i valori attuali delle unità di raffreddamento vengono trasmessi a moneo. Dai valori rilevati si possono calcolare i costi per il consumo di energia e di corrente, nonché le perdite di trasporto e di linea.
Risultato
Uso efficace ed efficiente dell’energia
L’ampliamento del monitoraggio del circuito di raffreddamento comporta due vantaggi principali: la temperatura del contenuto del serbatoio viene monitorata costantemente e il processo di fermentazione può essere controllato con precisione.
- Il consumo di CO2 per serbatoio può essere misurato partendo dai valori di processo forniti.
- Il processo di raffreddamento può essere utilizzato in modo efficiente e in base alle necessità.
Struttura
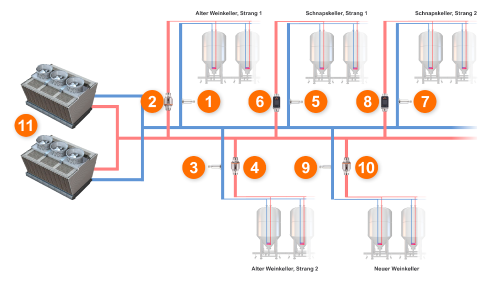
- Sensore di temperatura nella condotta di mandata - Vecchia cantina linea 1 - TA2417
- Sensore di flusso magneto-induttivo nella condotta di ritorno - Vecchia cantina linea 1 - SM9000
- Sensore di temperatura nella condotta di mandata - Vecchia cantina linea 2 - TA2417
- Sensore di flusso magneto-induttivo nella condotta di ritorno - Vecchia cantina linea 2 - SM9000
- Sensore di temperatura nella condotta di mandata - Cantina liquori linea 1 - TV7405
- Sensore di flusso magneto-induttivo nella condotta di ritorno - Cantina liquori linea 1 - SM8020
- Sensore di temperatura nella condotta di mandata - Cantina liquori linea 2 - TV7405
- Sensore di flusso magneto-induttivo nella condotta di ritorno - Cantina liquori linea 2 - SM8020
- Sensore di temperatura nella condotta di mandata - Nuova cantina linea 1 - TA2417
- Sensore di flusso magneto-induttivo nella condotta di ritorno - Nuova cantina linea 1 - SM2000
- Unità di refrigerazione
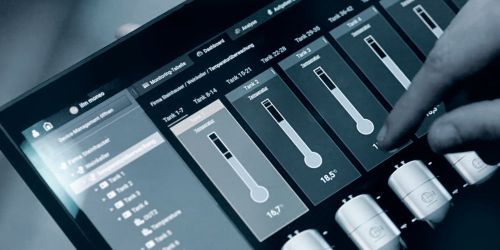
Il nostro cliente
La distilleria Steinhauser di Kressbronn, sul lago di Costanza, è un’azienda familiare che risale al 1828. Nel 1996, Steinhauser si è rinnovata e ora gestisce la più moderna distilleria vincolata d’Europa. I sensori ifm e il software moneo vengono utilizzati con successo dal 2021; i prodotti della distilleria sono stati premiati.
Struttura del sistema
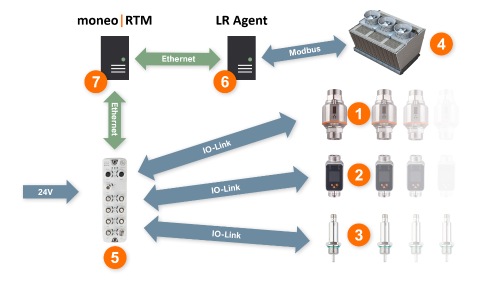
- Sensore di flusso nella condotta di ritorno - SM2000 / SM9000 (cantina nuova e vecchia)
- Sensore di flusso nella condotta di ritorno - SM8020 (cantina liquori)
- Sensore di temperatura nella condotta di mandata - TA2417 / TV7405 (cantina liquori nuova e vecchia)
- Unità di refrigerazione con interfaccia Modbus
- Master IO-Link - AL1353
- LR Agent (installato su un server)
- moneo RTM come appliance QHA210
Dashboard
La dashboard fornisce all’utente una panoramica dei valori di processo rilevanti per l’intero impianto di refrigerazione.
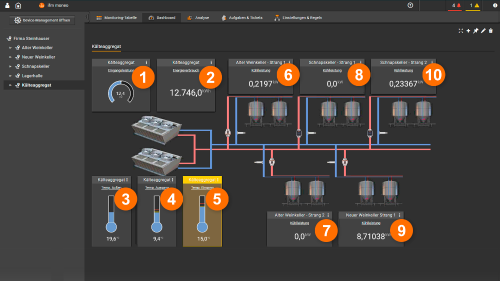
- Potenza di ingresso dell’unità di refrigerazione** (kW)
- Consumo di energia totale dell’unità di refrigerazione fino ad oggi** (kW/h)
- Temperatura esterna dell’unità di refrigerazione** (°C)
- Temperatura del refrigerante all’uscita dell’evaporatore dell’unità di refrigerazione** (°C)
- Temperatura del refrigerante all’ingresso dell’evaporatore dell’unità di refrigerazione** (°C)
- Capacità di raffreddamento - Vecchia cantina linea 1 CDS* (kW)
- Capacità di raffreddamento - Vecchia cantina linea 2 CDS* (kW)
- Capacità di raffreddamento - Cantina liquori linea 1 CDS* (kW)
- Capacità di raffreddamento - Nuova cantina linea 1 CDS* (kW)
- Capacità di raffreddamento - Cantina liquori linea 2 CDS* (kW)
* CDS (Calculated Data Source) indica un valore calcolato con moneo Data Flow Modeler
** I valori vengono letti tramite l’interfaccia Modbus dell’unità di refrigerazione
Questa dashboard fornisce all’utente una panoramica di tutti i valori di processo rilevanti dell’unità di refrigerazione.
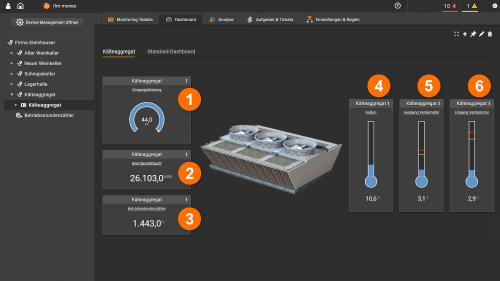
- Potenza di ingresso dell’unità di refrigerazione (kW)
- Consumo di energia totale dell’unità di refrigerazione fino ad oggi (kW/h)
- Contatore delle ore di funzionamento dell’unità di refrigerazione (h)
- Temperatura esterna dell’unità di refrigerazione (°C)
- Temperatura del refrigerante all’uscita dell’evaporatore dell’unità di refrigerazione (°C)
- Temperatura del refrigerante all’ingresso dell’evaporatore dell’unità di refrigerazione (°C)
La dashboard seguente fornisce all’utente tutti i valori di processo attuali del circuito di refrigerazione della cantina di liquori
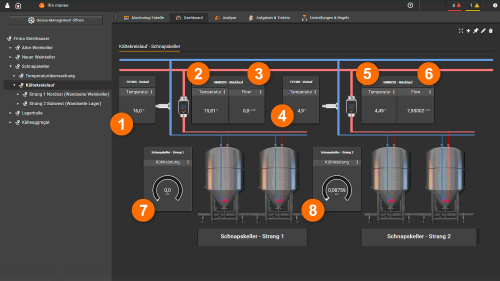
- Temperatura del refrigerante nella condotta di mandata - Cantina liquori linea 1 - TV7405 (°C)
- Temperatura del refrigerante nella condotta di ritorno - Cantina liquori linea 1 - SM8020 (°C)
- Flusso di refrigerante nella condotta di ritorno - Cantina liquori linea 1 - SM8020 (L/min)
- Temperatura del refrigerante nella condotta di mandata - Cantina liquori linea 2 - TV7405 (°C)
- Temperatura del refrigerante nella condotta di ritorno - Cantina liquori linea 2 - SM8020 (°C)
- Flusso di refrigerante nella condotta di ritorno - Cantina liquori linea 2 - SM8020 (L/min)
- Capacità di raffreddamento - Cantina liquori linea 1 CDS* (kW)
- Capacità di raffreddamento - Cantina liquori linea 2 CDS* (kW)
La dashboard "Nuova cantina - linea 1" fornisce all’utente una vista dettagliata della rispettiva linea di raffreddamento dell’impianto di refrigerazione.
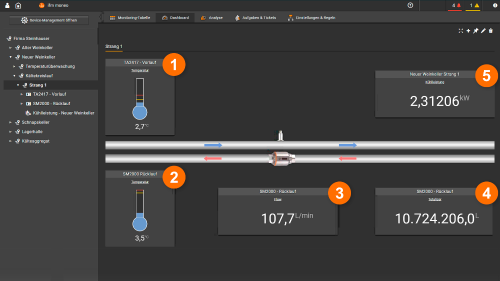
- Temperatura del refrigerante nella condotta di mandata - TA2417 (°C)
- Temperatura del refrigerante nella condotta di ritorno - SM2000 (°C)
- Flusso del refrigerante nella condotta di ritorno - SM2000 (L/min)
- Totalizzatore del refrigerante nella condotta di ritorno - SM2000 (L)
- Capacità di raffreddamento - Nuova cantina linea 1 CDS* (kW)
Vista dettagliata: sensore di flusso SM2000 nella condotta di ritorno Nuova cantina linea 1
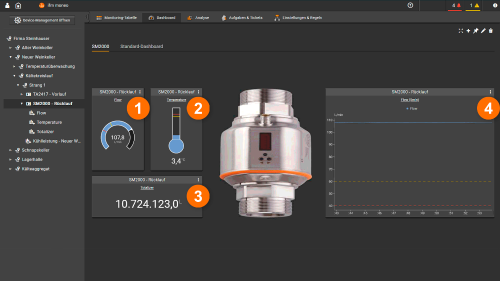
- Valore del flusso di refrigerante - SM2000 (L/min)
- Valore della temperatura del refrigerante - SM2000 (°C)
- Totalizzatore del refrigerante - SM2000 (L)
- Grafico a linee del valore del flusso del refrigerante - SM2000 (L/min)
Analisi
Ulteriori dettagli possono essere visualizzati tramite la funzione Analisi. La schermata mostra la relazione tra il valore della temperatura nella condotta di mandata e quello di temperatura e flusso nella condotta di ritorno del circuito di raffreddamento sulla linea 1 della nuova cantina
Calculated Values: valori calcolati
Oltre ai valori di processo dei sensori, all’interno di moneo è possibile calcolare molte altre informazioni.
Il "Data Flow Modeler" permette di creare valori calcolati definiti dall’utente, ad esempio combinando le origini dati provenienti dai sensori in un modello di flusso dati.
Calcolo della capacità refrigerante della linea 1 della nuova cantina
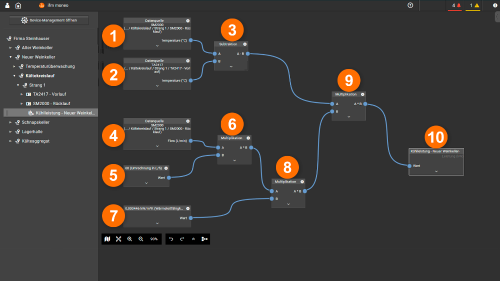
- Valore di temperatura del sensore di flusso SM2000 nella condotta di ritorno (°C)
- Valore di temperatura del sensore di temperatura TA2417 nella condotta di mandata (°C)
- Blocco funzione "Sottrazione" per il calcolo della differenza di temperatura
- Valore di flusso del sensore di flusso SM2000 nella condotta di ritorno (L/min)
- Costanti "60" per la conversione da litri al minuto a litri all’ora
- Blocco funzione "Moltiplicazione" per la conversione da litri al minuto a litri all’ora
- Costanti "0,000446" per la conduttività termica del refrigerante utilizzato (kW/m*k)
- Blocco funzione "Moltiplicazione" per il calcolo della capacità termica all’ora
- Blocco funzione "Moltiplicazione" per il calcolo della potenza refrigerante (kW)
- Risultato della capacità di raffreddamento della linea 1 nella nuova cantina (kW)