Kettec – With delicate precision against hurricane forces
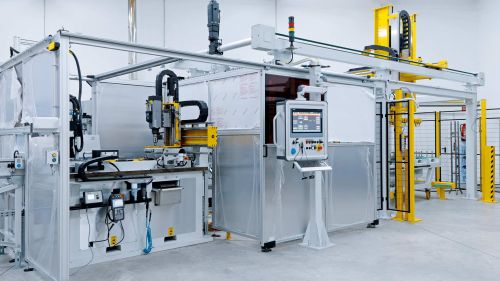
Fully automated machinery produces components for wind turbines
Wind power plays a key role in the transition from fossil- based to renewable energy production. It ranks second or third behind photovoltaics, depending on whether or not hydropower is considered a renewable energy resource and the production of electricity from wind is continuously increasing. In 2021, the capacity of all wind turbines worldwide increased by 94 gigawatts to almost 840 gigawatts. The companies Kettec and Tiskens contribute to the expansion of this segment of renewable energies by building plants that are as efficient as possible.
Modern wind turbines are up to 180 meters high and can produce up to six megawatts of electricity per hour at maximum capacity. For the turbines to be able to convert the wind energy into electrical energy with long-term and maximum efficiency, loss-free power transmission must be ensured. Here, the rolling bearings play a key role. The smoother they run, the lower the energy loss. Accordingly, the components used to manufacture each rolling bearing must be of the highest quality. One of these components is the rolling bearing cage, which keeps the balls in position and ensures loss-free power transmission.
0.2 millimetre tolerance over 19 metres
“The manufacture of these rolling bearings calls for enormous precision,” says Joachim Schmitz, Head of Sales and Development Mechanical Engineering at Kettec GmbH. The company specialises in the manufacture of automated special machinery. It was precisely this kind of machine a manufacturer of wind turbine bearings was in need for. “The machine we developed and built can weld together individual components fully automatically to form blanks of up to 19 metres for rolling bearing cages, all with a tolerance of only 0.2 millimetres.”


From the individual components supplied, a precisely dimensioned rolling bearing cage is to be manufactured (left). The fully automated milling and welding unit must work reliably and with highest precision (right).
Smooth automation of complex processes
Gripping, conveying, welding, milling: To make sure the entire, complex process runs smoothly and automatically with maximum reliability and precision, the sensors must be just as reliable and precise. “We have been working with ifm for ten years already,” says Joachim Schmitz. “Their extensive range and product quality had us convinced right from the start. Accordingly, the current machine contains many components from this provider of automation technology and digitisation solutions. They ensure that the complex, interconnected processes function just as smoothly as the ball bearings in which the rolling bearing rings will be used later.
Safety solutions from a single source
The first step, the loading of the individual components into the system, is done manually. For this purpose, a transport trolley is positioned and fixed underneath the gantry robot. But not only the presence of the trolley is detected with sensors: Safety light grids also prevent the gantry robot from moving while persons are in the danger zone. To allow operators to work safely underneath the gantry robot, two inductive safety sensors detect whether the gantry robot has assumed a safe position and is additionally secured with a bolt.
“In addition to ifm’s safety sensors, we will also use their Safety Service in the future – for us as plant developers, it is a great advantage to obtain all automation aspects and components from a single source,” says Joachim Schmitz. The ifm Safety Service assists plant manufacturers in developing and implementing a seamless, legally compliant and state-of-the-art safety system.


Where manual work meets automated work, operators must be reliably protected by safety precautions (left). Besides safety products, such as its inductive safety sensors, ifm also provides advice and support through its Safety Service (right).
Length detection to the tenth of a millimetre
Once the individual parts have been placed under the gantry and all persons have left the secured area, the system takes over. Presence detection, pick-up and correct orientation of workpieces, completeness check of milling attachments, exact manoeuvring of the gripper on the gantry robot, and precise positioning of the milling and welding unit: “Everything that can be moved and detected automatically in the system is solved by means of ifm sensors,” says Joachim Schmitz. The same applies to the precise length measurement of the rolling bearing blank. “For this task, we use an absolute multiturn encoder in combination with a measuring wheel. Thanks to the high resolution and the accuracy of 0.1 degrees, we can reliably meet the stringent tolerance specifications.”



Inductive sensors detect the presence of the milling heads (left), a light barrier ensures exact positioning of the workpieces before welding and an absolute multiturn encoder is used for precise length measurement (right): For all these tasks, Kettec relies on sensor technology from ifm.
Permanent and precise position monitoring
The advantage of absolute multiturn encoders such as the RMV300 used here is that they can track the absolute position even in the currentless state and transmit any changes once power is supplied. “If our workpiece is displaced in the currentless state, we still know the exact length of the bearing cage blank that has been welded so far,” says Joachim Schmitz.
The many benefits of IO-Link
All sensors of the special machine communicate via IO-Link – a significant advantage, as Jan Tiskens, Technical Sales Engineer at Tiskens Steuerungs- und Antriebstechnik GmbH & Co. KG knows. The company implements the automation for Kettec. “A great benefit for our work is the fast, easy, and error-free wiring,” says Jan Tiskens. “It allows us to save up to 20% of the time compared to conventional central wiring. In terms of individual customer solutions, we are also more flexible if we want integrate additional sensors for enhanced functionality which were not originally considered in the planning. All this is much easier to achieve thanks to the decentralised approach. At the same time, we save around 15% of cabling costs because we can connect the field-compatible IO-Link masters in series, minimising the need for long cable runs.”


The PerformanceLine IO-Link masters, here with Profinet interface, facilitate and accelerate the connection of sensors and provide sufficient power supply for actuators.
Remote diagnosis can reduce downtime
The decentralised, digital connection of the sensors is not only beneficial for initial implementation of the automation. “Thanks to remote maintenance, we can check the entire system down to the individual sensor for proper function and faults, and do not have to wait with troubleshooting until we get to the customer’s site,” says Jan Tiskens. “We can identify the cause in advance from our location. This also drastically reduces any further maintenance work that may be required at the customer’s site. Defective cable sections can be replaced without causing serious downtime, and even sensors can usually be replaced with limited expertise, i.e. by the customer’s own staff, as the IO-Link master will automatically transfer the stored parameters to the new sensor. This can significantly reduce downtime.”
Digital quality assurance
And finally, the digital acquisition of all process data leads to a considerable gain in comfort and safety for the end customer, as Joachim Schmitz emphasises: “All data is documented with a time stamp. In the event of a recourse claim, it can be verified easily and unequivocally whether actual deviations occurred in the process which affect the quality of the end product.”
Conclusion
With its broad range of modern sensors and infrastructure solutions, ifm supports the companies Kettec and Tiskens in automating and digitising even complex and unique pro- duction plants. Not only the companies, but also the end customers benefit from the advantages of digital data transmission via IO-Link.