Migros – Vast improvements in efficiency in determining material requirements
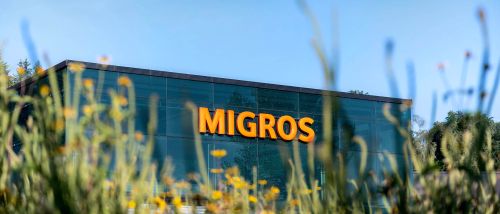
Process optimizations at all levels are crucial for retail stores, if they are to hold their own in the fierce retail war against their e-commerce competitors. To streamline its ordering processes, a Swiss retail group has implemented a SAP-certified software solution for optimizing logistics processes in SAP. This software brings a host of advantages for buying – for example, through bundling purchase orders, monitoring restrictions for optimized loading equipment planning, and automatically generating range-oriented purchase order quantity recommendations. This prevents expensive media disruptions and enhances the process quality and reliability in demand planning. In combination with applications for daily operations and controlling, this gives the retail outlet chain a high-performance software for an efficient supply chain.
Retailer Migros is a conglomerate of various co-operatives, corporations, and foundations, which refers to itself collectively as the “Migros community”. The group is represented externally by the Migros-Genossenschafts-Bund (the Federation of Migros Cooperatives, MGB). Migros is the largest retail company in Switzerland.
With a fulfilment center and several distribution centers, the centrally organized ERP (ZWW) facilitates the rapid delivery of goods to more than 1,000 retail outlets. This means that the ordering processes need to be as efficient as possible, in particular if the company is to remain competitive as a stationary retailer in the face of the growing e-commerce business sector. Swiss retail outlet chain Migros achieves this with the help of the GIB Suite from Siegen-based GIB mbh. The suite is SAP-certified and seamlessly supports all logistics processes in SAP, where it provides for greater transparency and efficiency.“ The GIB Suite has enabled us to create a level of transparency that has been extremely well-received by demand planners, administrators, and managers alike,” says Urs Schwarzenbach, Head of Management Support for Near/Non Food at Migros.
Solution integrated in the SAP standard
Schwarzenbach was involved in the implementation of the GIB Suite in fall 2014. The first applications to be implemented were ‘Operations’, for daily operations, and ‘Buying’, for order processes; just a few months later, the ‘Controlling’ application was added to the solution. GIB even developed the ‘Buying’ application in-house in cooperation with Migros. “This enabled us to achieve vast improvements in efficiency in terms of determining material requirements and facilitating job cover among employees,” explains Schwarzenbach. “We were also able to increase availabilities in the distribution centers, thanks to a simultaneous reduction in storage volumes.”
MGB is therefore extremely happy with the solution and solution provider. “We first got to know GIB through a seminar,” recalls Wieland Caviezel, SAP consultant at Migros.
The co-operative’s target requirements were to integrate a solution in the SAP standard, so as to avoid media disruptions, and to improve the efficiency of materials planning in ERP with a system-supported tool that offered the option of using the existing SAP master data and parameters.
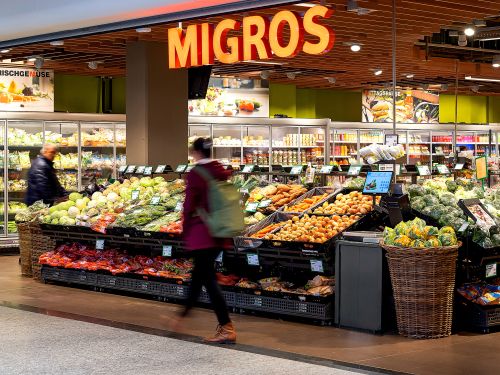
Measurable success
“We achieved all our main aims listed in the project proposal with regard to improving the efficiency of merchandise planning (goods procurement, demand planning) and reducing storage costs,” says Schwarzenbach. “The increase in availabilities in the distribution centers, thanks to a simultaneous reduction in storage volumes, is also clearly noticeable.” It has also been possible to optimize stock levels and purchase order quantities, since the correct quantities (according to range, rounding quantity) can be restocked on the purchase order monitor for the ‘right’ products (ABC, life cycle), if the truck or Far East container is not completely full. In addition, the slow-moving issue has significantly improved; this has been most evident for ‘slow-moving items’ in the clothing and household goods categories.
One of the biggest efficiency gains brought about by the tool is, however, the increase in transparency. While demand planners used to maintain master data in their own/a separate Excel list, they now manage their master data in SAP, resulting in greater transparency, thereby making it easier for employees to cover each other. Thanks to up-to-date master data and KPIs, it is also easier to make and understand materials planning decisions.
Less need for training, thanks to high user-friendliness
The implementation of the GIB Suite, plus various Migros-specific adjustments, such as Migros tabs, ad-hoc formulas, and enhancements via exits, by a project team of 10 employees from GIB and Migros went smoothly and was accompanied by two personal two-hour training sessions with key users. “The project members created the relevant training documents themselves. This ensured that the implementation phase went smoothly and the suite could be used just a few hours after the training session,” says Schwarzenbach.
Fazit: No going back
No one knows now how they ever managed without the software solution. MGB believes that the GIB Suite in particular scores points for effectiveness – in the sense of ‘doing the right things’ – and working optimally, thanks to comprehensive information, ranges and range optimization, and the option to call up management ratios in a variety of views (e.g. Sale/Forecast). “In particular the applications ‘Operations’, for carrying out daily jobs such as identifying pre-allocated stock, complaining about supplies, maintaining master data, etc., and ‘Buying’, for determining material requirements and releasing purchase orders, offer the biggest benefits for our day-to-day business,” adds Schwarzenbach.
The time saved thanks to the GIB software as a result of greater transparency and efficiency enables Migros to concentrate on other important tasks. The company is now already planning further joint projects with GIB. For example, Migros has implemented a series of change requests with the IT service provider and is planning for the future: “We’re sure that S/4HANA is going to offer a great deal of potential in the future for our further collaboration with GIB,” says Caviezel.