Stellantis S.p.A – ifm solutions for condition-based maintenance in the FCA plant in Verrone (Italy)
Giuseppe Mottola, WCM Plant Support Stellantis S.p.A., introduces the FCA plant in Verrone and points out the numerous awards, including the World Class Manufacturing Gold level, one of the highest international acknowledgements.
The plant also received the renowned international "Lean & Green Management Award" from two German consulting firms, which evaluate a group of companies each year on the basis of the so-called "Lean Production" that ensures an efficient management of energy and environmental resources, plants and logistics.
ifm is a partner of the FCA plant in the area of condition-based maintenance. The cooperation was formed with the goal of improving the quality of the production process and saving costs for the plant. For time-based maintenance, which used to be employed by the plant, the machines had to be stopped, so that the maintenance technicians could conduct a vibration analysis.
The advantages of condition-based maintenance are avoiding standstills, optimisation of time and reduction of failures. This cuts the costs for the benefit of plant efficiency. The condition-based maintenance enables an exchange of components in the machine before a failure takes place. While maintaining the same degree of reliability, it is possible to reduce the costs for a preventive maintenance and to make use of the full operational lifetime of the components, explains Riccardo Marino, Maintenance Engineering Manager Stellantis S.p.A.:
In addition to vibration monitoring on all relevant machine axes, ifm devices monitor flow, temperature and pressure of the coolant in the mentioned production line.


Picture 1: Flow and pressure sensors from ifm. Picture 2: Diagnostic units for vibration sensors, IO-Link master CabinetLine and LED display for the signal conversion of analogue measured values via IO-Link

World Class Manufacturing Gold level for the FCA plant in Verrone

Vibration sensors from ifm
A high standard of quality in production
The advantage is therefore not only that possible damage can be detected at an early stage, but also maintaining a high quality standard of production. Given the strategic importance of this process regarding the quality of the final product, the line described above was selected.
The LINERECORDER SMARTOBSERVER software from ifm for the storage of data, predictive maintenance and energy monitoring, controls and communicates the behaviour of connected machines. Possible warning and alarm messages are sent via email, so that an intervention can be planned without delay. Machine Learning enables assessing the state of the machine and, if necessary, taking action before errors occur.


Picture 1: View of the pumps in the LINERECORDER SMARTOBSERVER software from ifm. Picture 2: View of machine tools controls in the LINERECORDER SMARTOBSERVER software from ifm.
Eduardo Vassallo, Maintenance Engineering Specialist Stellantis S.p.A. explains: "The machine 'talks to us'; thanks to alarm signals, whenever the current value surpasses the set limit value, we receive a notification and are able to intervene."
The cooperation between the design engineers from FCA and ifm supported the project throughout all phases - from development on to installation and setup.
Diego Ceriotti, Professional Maintenance Specialist Stellantis S.p.A., says: "We are using the same ifm system for autonomous maintenance as well and are also planning to implement it for monitoring and remote management of technical systems, for example central filter systems."
Condition-based maintenance is one of the basic elements of Smart Factory, a current concept of big importance, which is to strengthen the cooperation between FCA and ifm.
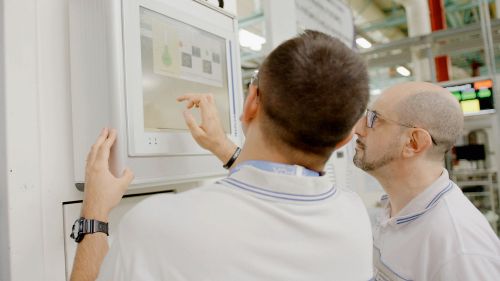
Use of the panel PC for monitoring autonomous maintenance
Conclusion
Leonardo Rossi, Plant Manager Stellantis S.p.A., adds: "I am convinced that Industry 4.0 and the development of World Class Manufacturing are closely related; in the future we would like to work more on this matter in cooperation with ifm in order to meet the new challenges of our company."