Keeping the filling process running
How breweries and beverage producers can meet the current challenges
Efficient, resource-saving and sustainable production with constantly rising energy and raw material costs and an increasingly "volatile" sales market: In a nutshell, these are the challenges that breweries and beverage producers have to face. But the bad news is immediately followed by good news: There are at least as many solutions as challenges. A powerful software rolled out from shop floor to management level addresses several of these issues. At BrauBeviale (ifm booth 121, hall 6), such solutions, that are precisely tailored to the requirements of the beverage industry, will be presented.
By: Gerald Scheffels for ifm
Focus on energy and resource efficiency
The cost factor of energy alone is currently enough to cause problems for breweries or beverage producers. This is because many steps in the production process (mixing, cooling, aerating, conveying, filling, palletising...) are energy-intensive and, with the limited margins customary in the industry, energy price increases can quickly jeopardise the profitability of production – especially as the costs of raw materials and expendable supplies are also rising.
In addition, compressed air is used for many processes in beverage production, such as drying, cleaning or sorting, which is known as a flexible form of energy that can be used very well under hygienic conditions, but is also expensive. Typically, compressed air generation and treatment accounts for 10 to 30% of a company's total energy costs, and these costs are usually in the millions.
New regulations and obligations
But that’s not all: Like other companies in the food and process industries, breweries and beverage producers are being called upon to further develop their production in the direction of sustainability. This includes reducing the consumption of fossil fuels, minimising waste and greenhouse gas emissions as well as saving water and energy. In addition, new regulations relating to sustainability must be put into account; e.g. on the (preferably renewable) packaging materials used.
Another challenge is the increasingly intensive reporting obligation. Currently, for example, the CSR Directive needs to be implemented and a company-wide carbon footprint needs to be documented.
Digitalisation brings the solution
These issues – energy costs, sustainability, and reporting obligations – are interrelated and reinforce each other. But you can also look on the bright side: Breweries or beverage producers that actively tackle one of these challenges will potentially also notice positive effects on the other fields of action.
It is not surprising that digitalisation is the key to mastering these tasks (reducing costs, increasing efficiency, minimising resources, etc.). At the “hardware” level of processes, most large and small companies in the brewing and beverage industry are already well positioned. But at the level of data and information and their analysis, there is still considerable potential for users to realise sustainable improvements, e.g. in terms of yield.
Data (and its analysis) is the key
What can be achieved through smart and “customised” digitalisation? Here are some examples from the brewing and beverage industry:
- Online energy monitoring leads to a sustainable reduction in energy consumption.
- Real-time information from the manufacturing or filling process increases system availability.
- Precise process control increases the yield and resource efficiency as well as the (always consistent) product quality.
- The automation of ordering transactions, warehouse management and materials planning enables demand-driven production and thus avoids waste of resources.
The benefits of IIoT technologies
Using IIoT technologies to monitor machines and systems based on real-time information is particularly effective. This makes it possible to optimise the supply chain and make quality control more closely meshed and therefore more efficient. AI-based solutions will open up even greater optimisation potential in the future.
Increase efficiency with consistent data flow
It is equally important that the data collected by the sensors at "shop floor" level (temperature, pressure, flow rate, etc.) is not only used "in the loop", but also passed on to the SAP ERP system and processed. This is because actions can be carried out immediately – for example, the timely scheduling of maintenance personnel or the precise triggering of spare parts orders. By analysing and consolidating the data and information, it is also possible to identify where disruptions repeatedly occur or scrap is produced. Among other things, this helps to avoid unplanned machine downtimes/production standstills and waste. The prerequisite for this is using a software solution that is ideally matched to the sensor technology and seamlessly integrated into the SAP ERP system. When intelligent sensor technology and sophisticated supply chain software come together, the result is unprecedented transparency. This is exactly what can be achieved with Shop Floor Integration (SFI) from ifm.
Automatic replenishment control for acid and caustic tanks
A concrete example: Hygiene is the top priority in the beverage industry. Each bottle must be thoroughly cleaned before filling. Hot lye is often used for this, which is pumped directly into the washing system from storage tanks. If the tank is empty, the cleaning process stops and all subsequent production steps come to a standstill. To prevent this worst-case scenario, it must be ensured that there is always enough replenishment. Sensors can be used to measure the fill level in the tank. However, it only becomes efficient when the information is not only available at the machine but also flows directly into the SAP ERP system. This is where Shop Floor Integration comes into play. SFI links the sensor-determined fill level values with SAP so that relevant follow-up processes such as replenishment control are triggered automatically. The stored data can also be used directly for evaluations or reporting to identify and exploit optimisation potential – this keeps the filling process running.
BrauBeviale – MEET US!
International trade fair for the production and marketing of beverages
Visit us in November at BrauBeviale in Nuremberg and find out more about the benefits of our SAP-based software tools for the beverage industry – booth 147, hall 6.
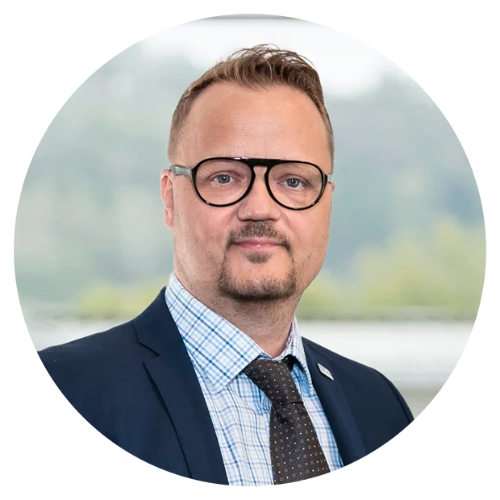
Peter Schwarz
Head of Business Development
& Indirect Sales, GIB S&D GmbH