ZF Friedrichshafen AG – Better drive in SCM for automotive suppliers
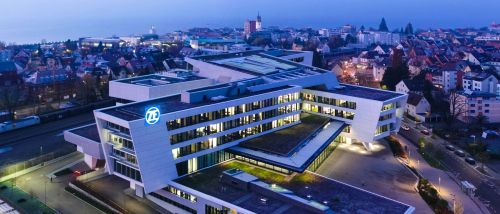
ZF forum in Friedrichshafen (© ZF)
SAP add-on for optimising material requirements planning and inventory controlling
To be able to manage global value chains and different business units in such a way that loss-makers can be identified quickly and investments can be made in the right place at the right time, internationally established companies need efficient and transparent processes. With this in mind, the globally active automotive supplier ZF calculates and optimises its logistics processes in SAP with ifm's SAP-certified supply chain solution. The software modules used support the company in its demands and inventory-optimised controlling processes and aid them in achieving the best possible management of the entire company through cross-national and cross-plant transparency.
Improving functionality and performance
ZF's product portfolio covers technologies for improving drive efficiency, vehicle safety and reliability, and automated driving. Against this backdrop, it is only logical that the technology leader is also focussing internally on efficient, secure and automated processes.
A few years ago, Udo Wessbecher, Head of IT Supply Management Inbound at ZF Friedrichshafen, became aware of the SAP-based software from ifm (formerly GIB). By using the so-called "GIB Suite", numerous national and international companies have already improved their process management and controlling sustainably and effectively. As they sought to initiate implementing their own improvement and optimisation goals, ZF showed an interest in the software. By this stage, the software programs used by ZF were already running up against their capability limits. Various self-written analysis tools were struggling with performance problems.
“The GIB Suite was the optimal solution. We planned to implement the analysis software globally. “Due to a lack of functionality, this would not have been possible with the in-house developed solution,” recalls Udo Wessbecher. Meanwhile, the automotive supplier uses the GIB Suite modules Operations, Controlling and Planning.
Efficiency advantages through uniform group standard
In 2011, the Operations module was first introduced in one plant and then successively rolled out in numerous plants and country locations. “We aimed to get an overview of all relevant materials planning information by using Operations and to take advantage of the new-found transparency to make day-to-day work easier and to control it in a targeted way,” explains Wessbecher. “That is precisely what happened.”
Modern and intuitive user interfaces that enable fast and clear navigation were also important to the automotive supplier. To enable a quick and smooth use of the two GIB Suite modules Operations and Controlling, the users learned in training sessions how they can ideally apply the software to their workflows.
The Controlling module is used worldwide at ZF today. After an intensive performance audit and a comparative analysis involving six other solutions, it was gradually rolled out in 150 plants across the globe. “Particular aspects such as functional scope, flexibility and costs of the solution as well as the provider’s expertise were crucial factors in our decision-making process,” says Wessbecher.
The Controlling module ensures inventory-optimised purchase orders and a significant increase in delivery readiness through group-wide transparency. “With the tool, we have managed to create a uniform group standard,” says Rainer Grimm, IT Supply Management Inbound at ZF Friedrichshafen. “That way we can guarantee the same controlling methodology worldwide.”
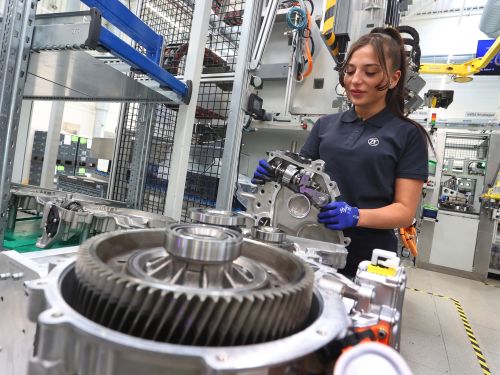
Assembly Electric Axle Drive, Production location Schweinfurt (© ZF)
Communication on an equal footing
At the technology group, a similarly positive outlook can also be reported from investment and procurement. From a corporate perspective these have brought crucial benefits, in particular by enabling standardised controlling processes and, at the same time, by introducing intuitive user interfaces.
The ZF implementing team emphasises that the delivery of the software solutions also accompanies a transfer of expertise. “During the communication between the solution provider and the professionals from materials planning, controlling and supply chain management, it became clear: experts are talking to experts here,” says Wessbecher. The practical relevance of the ifm employees has also helped to ensure that the implementations that have long since been completed today have been successful and that a similar outcome can be expected for upcoming projects.”