Monier Roofing Components roofing component manufacturer implements SAP add-on for optimised process control and controlling
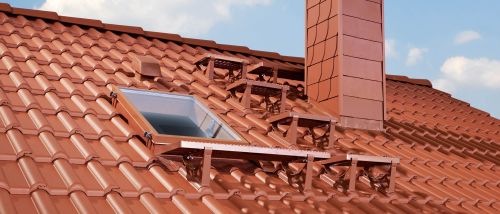
The Dispo-Cockpit for better cost effectiveness
Globalised markets, internationally active enterprises and increasingly stiff competition: factors that require companies to secure their future competitiveness starting at the process level. That is why a roofing component manufacturer has chosen the GIB Dispo-Cockpit, an SAP-certified add-on for the optimisation of logistics processes in SAP, so as to be able to respond quickly and effectively to changing market conditions. The Dispo-Cockpit modules allow not only for ordering that is exactly tailored to requirements and stocks, but especially for inter-factory transparency and therefore for the best possible running of the entire company.
Transparent processes
We have several production facilities, so transparent processes are extremely important for us, for instance in order to be able to carry out precise analyses across all factories, explains Marijana Duvnjak, Supply Planning Manager at Monier Roofing Components GmbH. That was not satisfactorily possible with our previous standard SAP solution for stock management, production planning and stock optimisation. Therefore the company relied on additional Excel-evaluations to aid stock management and production planning. Especially appraisals for analysis and optimisation of stocks, coverages as well as slow movers and non-movers required a large amount of manual work. Also, the standard SAP software was unable to provide analyses, key parameters and graphic evaluations to provide a basis for operative and strategic decisions on a day-to-day basis.
In view of this, Monier Roofing Components GmbH began to search for software that was capable of optimising its existing SAP processes, especially regarding transparency and clarity. Following a call for tenders, the decision was taken in favour of a solution from GIB. GIB was awarded the contract not least because the standard SAP Controlling and Operations add-on modules already fulfilled a large proportion of our requirements, as Marijana Duvnjak points out. Ms Duvnjak is also the project manager responsible for integrating Dispo-Cockpit.
Currently, the company is successfully using four modules: Dispo-Cockpit Controlling (DCC), Operations (DCO) and the Planningmodule (DCP) were implemented early in 2013. Then, in the spring of 2014, Dispo-CockpitForecast(DCF) was added. All four modules are closely integrated with each other, and they are used at headquarters as well as all the various production facilities. Whereas DCC, DCO and DCP could be launched pretty well as plug-and-play installations, integrating the turnover planning and forecasting module (DCF) proved to be the most time-consuming job on account of the complex, customer-specific requirements.
A birds-eye view from the Cockpit
A further benefit provided by the Dispo-Cockpit modules is the all-encompassing overview of all relevant data and facilities. It is now considerably easier to draw up cross-factory analyses, so that stocks and order quantities could be optimised. Now each materials requirements planner can check, modify and monitor stocks and order quantities directly and efficiently.
Marijana Duvnjak explains: We were already working on optimising the stocks and order lot quantities in parallel with the introduction of the Dispo-Cockpit. Now, though, by using the add-on we can address and implement optimisation potential closer to real time. The tool is managed from the perspective of a central cockpit. The user benefits from this by being able to access currently important decision-making information directly from the program without the need to open several different applications.
As the tool greatly facilitates its users daily work, it is correspondingly highly appreciated also thanks to the flanking key user training programme. Albeit one should not assume that an initial training and the rollout are sufficient when it comes to introducing such tools, Marijana Duvnjak points out. It is very important to maintain employees motivation to use the Dispo-Cockpit, to demonstrate the advantages and also to check on how the tool is being used, and offer further training as required.