Efficient compressed air monitoring with intelligent flow sensors
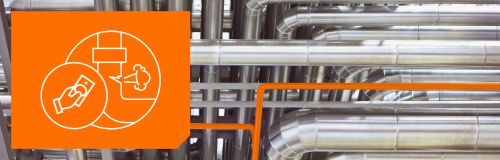
Do you monitor your compressed air systems? Discover an easy way to save a lot of energy!
Are you sure that your plant is not running out of air?
The competitiveness of a company is directly related to the energy efficiency of its plants and systems. The generation and distribution of compressed air is the second largest source of energy costs. Efficient leakage monitoring and leakage location are essential parts of energy monitoring and offer benefits in terms of reduced electricity costs, sustainable production and eligibility for statutory funding. The energy savings also allow for competitive advantages through reduced production costs.
Compressed air is not free
Undetected leaks at joints, connection points or non-functioning components can cause extremely high costs every year. The generation of compressed air can account for over 30% of an industrial plant's electricity consumption. Would you like to know what this means for you in practical terms? With small investments and government funding, you can ensure permanent and simple energy savings and allow for condition-based maintenance of your plants. Together with our experts you will find the right solution for your production. Call us:
Discover the advantages of efficient compressed air monitoring with ifm. In the digital machine hall, our experts discuss topics such as:
- Detailed consumption measurement on the end machine – from hardware to software (0:00-19:17)
- Compressed air monitoring on the distribution line – cost and leakage attribution made easy (19:17-31:50)
- Recording of key energy figures and compressor efficiency calculation (31:51-35:59)
Why compressed air monitoring?
Sustainability Increased energy efficiency and improved eco-balance Protection of valuable machines from too high/low supply |
Cost savings Less energy consumption when emission prices are rising Tax savings and statutory funding |
Certification The basis for an energy management system according to DIN EN ISO 50001 |
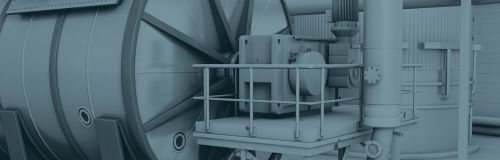
Compressed air is used in almost all industries. From the forge to the clean room - leaks can occur in any compressed air network. Compressed air monitoring systems and sensors are used in a wide variety of plants and machines. See our success stories for yourself:
Your potential with flow sensors from ifm
- Modular concept – from the main line via spurs to the end machine
- System solution – from the individual sensor to the control system to the cloud, everything from a single source
- One device, four process values – totaliser, flow, pressure, temperature
- Return on investment – reduced energy and maintenance costs, tax savings, funding
One device, four process values, countless advantages through IO-Link
The SD flow sensors from ifm precisely provide all process information required for the efficient use of compressed air and industrial gases. Whether flow rate measurement, pressure measurement, temperature monitoring or total quantity - you can monitor the process data with just one cable and one sensor. Accuracy losses due to electrical conversion losses are a thing of the past. You can view the status of your sensor at any time - even wirelessly while you are on the move. These and many other advantages are offered by using the SD sensors with IO-Link.
Real-time analysis Identify long-term trends about consumption or fluctuations of air pressure with the SD sensors and optimise processes |
Less hardware IO-Link transmits 4 values via 1 cable. Without additional sensors, cables or pipe fittings |
Wireless monitoring Mobile parameter setting, monitoring and recording of systems and processes with the IO-Link Bluetooth adapter |
Parameter setting Easy and fast parameter setting with the moneo configure software and IO-Link master |
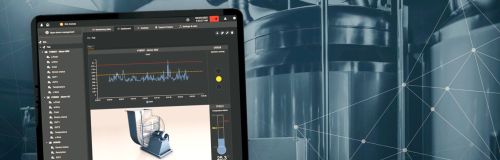
Permanently optimising the performance of machines and plants without neglecting the high quality standards of production - ifm system solutions enable maximum efficient production processes and ensure continuous diagnosis and early detection within your compressed air network. Benefits from individual condition monitoring solutions and predictive maintenance:
- Reducing costs
Condition-based maintenance when required instead of fixed service intervals. Replacement of parts can be planned. - Avoiding unplanned downtime
Vibration analysis and early detection of bearing damage to the engine's compressor. - Easy integration
Implementation irrespective of the in-house IT - individual application solutions from the sensor via the evaluation to the network-capable analysis tool. - From the sensor to the ERP
Scalable extensions to other applications or communication with ERP systems are possible.
Following the EU directive on energy efficiency DIN EN ISO 50001, all member states have committed to energy savings. Calibration of the sensors according to ISO or DAkkS standards is the basis for compliance with this guideline. Regular recalibration ensures the error-free and reliable function of your measuring equipment in the long term.
Get your personalised advice now!
Find out more about the savings potential and other advantages of ifm flow sensors. Start your energy saving project!
Write to info@ifm.com and our experts will be happy to call you back, or you can call us directly - at 0800 16 16 16 4.