- Flow sensors
- Products- innovations
- SU ultrasonic flow meter
Measuring flow with ultrasound
Precise flow measurement of applications with ultra-pure water, water and water-based media with up to 10% additives
The SU Puresonic detects flow rates of up to 1000 l/min with high precision. Thanks to ultrasound technology, this also applies to ultra-pure water with low conductivity as produced in reverse osmosis plants. The signal strength, which can be used as a quality and maintenance indicator, is also continuously detected.
The measuring pipe of the SU Puresonic is made of stainless steel and is free of measuring elements, seals and moving parts. This means that faults due to damage, leaks or blockages are excluded from the outset, as are design-related pressure drops.
The SU Puresonic in detail
What our customers say
“TheSU convinces with its stainless steel measuring pipe, which is free of measuring elements, seals and moving parts. This means that faults caused by deposits or wear are excluded from the outset, as are design-related pressure drops.”
Maximilian Meurer, Measurement and Control Engineer at EnviroFALK
“With the SU, we are able to precisely and accurately monitor the fresh water supply to the washing machines at sea and regulate the water volumes accordingly.”
Plant builder of laundry systems
“We previously used magnetic-inductive flow sensors and occasionally had to deal with error messages caused by very fine metallic particles in the water. Thanks to the SU Puresonic, we no longer have this problem.”
Daniel Kaltenbach, Fluidics Design Engineer at EFD Induction GmbH
“Theoutput of the signal strength allows conclusions to be drawn about contamination or process changes. Process changes are also indicated via the operating status LED and output via the diagnostic output. This way, maintenance measures can be taken at an early stage and downtimes can be prevented.”
Plant builder of coolant systems
Use cases
Precise flow measurement in water treatment
For more than 30 years, EnviroFALK GmbH has been designing, manufacturing and selling pure and ultra-pure water systems for a wide range of industries worldwide. Reverse osmosis is an essential process step in water treatment. In reverse osmosis, the supplied soft water is filtered into pure water. A relevant parameter for the customer is the quantity of pure water available at the end of the treatment process. Based on the flow rate, the plant operator can see, among other things, whether one of the membrane filters used requires maintenance.
To measure the flow, the customer uses the SU Puresonic ultrasonic sensor, which can detect flow rates of up to 1,000 l/min with high precision. Thanks to the ultrasound technology used, this also applies to pure and ultra-pure water with low conductivity as it is produced in the plants at EnviroFALK. In combination with the conductivity sensors of the LDL family, reliable control of the quality and quantity can be established in the filtration process.
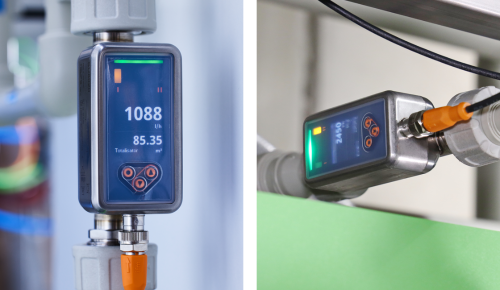
Regulation of water quantities in parts cleaning
A customer of ifm, a manufacturer of automated laundry technology, builds systems for the entire laundry process. These include washing machines used on cruise ships.
The technically treated seawater used to supply fresh water to the machines places special demands on the flow sensors used. The reason for this is the low conductivity of the water, which pushes classical measuring principles, such as the magnetic-inductive measuring principle, to their limits.
The SU Puresonic, on the other hand, can be used without any problems at low conductivities, as is the case with ultra-pure water, due to its ultrasonic technology, and can reliably monitor the fresh water supply. Besides, the magnetic-inductive sensors of the SM series are used in industrial water, in which there is an increased formation of bubbles and foam due to the cleaning agent.
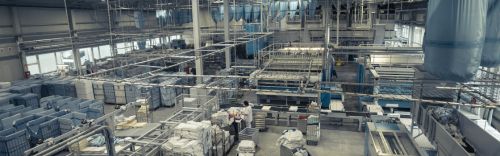
Trouble-free measurement even with metallic particles
EFD Induction GmbH has been developing induction heating solutions for over 70 years. The comprehensive product range at the Freiburg site includes induction hardening systems. In induction hardening systems, metallic components such as drive components for the automotive industry are inductively heated and then quenched with a water-based medium to achieve the ideal degree of hardness.
EFD Induction GmbH relies on the SU Puresonic to monitor the flow in the quenchant circuit of the system. Thanks to the ultrasonic measuring principle, the measurement is unaffected by the influence of very fine metallic particles in the water. Another advantage of the SU Puresonic is its component-free stainless steel measuring pipe, which is easy to clean if necessary. Besides, the output of the signal strength can be used to draw conclusions about the current level of deposits in the pipe system, which enables cleaning to be carried out as required.
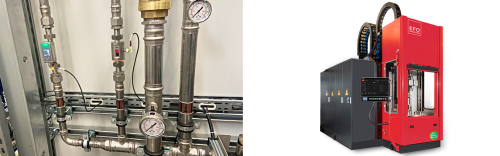
Use in cooling water supply
Cooling water systems ensure sufficient heat dissipation by means of water to guarantee the quality of the process and prevent wear of the tools. Especially in sensitive production processes, such as in the semiconductor industry, ultra-pure water is often used. The advantage: Corrosion and calcification in the pipe system are avoided, as are short circuits on electrical components.
In order to cool systems efficiently, the water flow must be detected precisely. In ultra-pure water systems, where the medium is characterised by low conductivity, ultrasound technology is best suited for measurement. A suitable sensor for this application is the SU Puresonic inline ultrasonic sensor, which detects flow rates with high reliability.
In contrast to a clamp-on device, the inline device does not require any calibration for an absolute measurement. Mounting-related errors that can affect accuracy are also minimised. The inline device also has the advantage of preventing faulty adjustments after installation that could be caused, for example, by inconsistent wall thicknesses or material properties of the pipes.
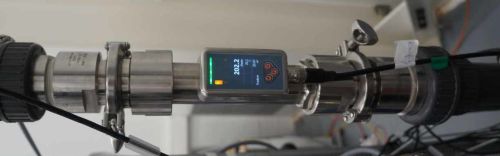
Condition monitoring
The permanently detected signal strength makes it easier to determine the maintenance requirements of the system at an early stage and thus minimise downtimes. The status of the signal strength can be read via the diagnostic output, via IO-Link or the operating status LED on the SU.
Flow | Temperature | Signal quality | Output 2 (analogue signal) |
Output 1 (diagnostics) |
|
---|---|---|---|---|---|
Green | normal | on | |||
Blue | low | off | |||
Red flashing | no signal | 3.5 mA // 21.5 mA | off |
In conventional wiring, it is not possible to distinguish between “low signal” and “no signal”, whereas all events are output in detail via IO-Link.
System connection
Added value thanks to IO-Link
- Transparent processes
In addition to the current flow, further information on the total quantity, the temperature, the device status and two switching thresholds are provided via IO-Link. - Condition monitoring
The signal strength (acyclic) provides an indication of possible contamination or process changes – maintenance measures can be taken at an early stage and machine downtimes minimised. - Loss-free data transmission
IO-Link enables loss-free data transmission: conversion losses are excluded via digital communication, and external influences, such as magnetic fields, have no effect on data transmission. In addition to loss-free data transmission, digital signals are characterised by improved accuracy and higher resolution.