Risse + Wilke – Retrofit your vehicles with collision protection
Forklift drivers need a high level of concentration when manoeuvring in reverse. The camera-based anti-collision system from ifm, which automatically detects persons and obstacles in the rear area of the vehicle, warns the driver and stops the vehicle, if necessary, provides support. The innovation: Existing vehicles can be easily retrofitted with this plus in safety.
Heavy forklift trucks transport the coils from the storage location to the rolling stand and back. Enormous masses have to be moved: The forklift trucks and their freight can weigh up to 30 tons. One steel sheet roll alone can weigh more than 12 tons. This means that the trucks' braking distance is quite a bit longer than that of a regular car.
Caution when manoeuvring
Particularly when reversing, e.g. after the coil has been picked up from the storage location or the rolling stand, the drivers need to be very cautious to avoid collisions with other forklift trucks or persons when turning into the lane. They do not only have to keep an eye on the rear area of the vehicle, but must also ensure that the carrying ram, with its load swaying from side to side, does not collide with anything.
Florian Rolf, production manager at Risse + Wilke, explains the enormous challenges the drivers have to face: "The forklift trucks are equipped with aids such as mirrors and cameras. Nevertheless, the drivers must still be fully alert at any time, they must always have 360° vision and monitor their load and where they are going. At the same time they have to be aware of what is happening around them, e.g. colleagues and contractors crossing their path. Otherwise it can easily come to critical situations which we want to avoid."

Special coil forklifts transport loads of several tons. A high level of concentration is required from the drivers due to limited visibility.
Collision warning system
In order to avoid such critical situations, the sensor specialist ifm from Essen has developed an automatic collision detection system.By means of a 3D camera, the system permanently monitors the rear of the forklift truck and gives the driver visual and acoustic feedback. Depending on the configuration level, the assistance system can even stop the vehicle, if necessary.
All obstacles are reliably detected. Thanks to a special classification of reflective materials, e.g. reflective vests or clothing, the collision warning for persons can be given priority over other objects. This increases the safety of persons and leaves the driver enough time to slow the truck down and stop in time. This provides maximum safety when manoeuvring.
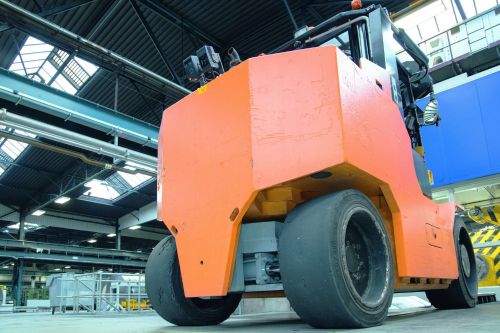


Picture 1:The 3D camera of the anti-collision system is mounted at eye level and monitors the rear area of the forklift truck. Picture 2: Persons behind the forklift truck are difficult to see for the driver. The anti-collision system helps to avoid critical situations when reversing. Picture 3: The driver sees the rear area of the forklift truck on the monitor. Colour-graded frames indicate objects in the path and display further warnings up to an e-stop.
Easy retrofitting
ifm offers the anti-collision system as a ready-to-start application package (order no. ZZ1103). The package includes all components to set up a fully functioning collision warning system on a mobile machine, e.g. a forklift, wheel loader, excavator, reach stacker or transport vehicle within a few minutes. In addition to the camera, the monitor and the controller, the package contains all necessary cables and mounting accessories. This means it can be easily retrofitted on all mobile machines with 24 V on-board system voltage.
Commissioning the system is very easy: After mechanical installation of the system and plug & play wiring, set-up is carried out within a few minutes via the pushbuttons and the colour display of the control unit. Only a few parameters (height and inclination angle of the camera, vehicle width) are required in the intuitive set-up process. Then the system is ready for operation. In contrast to other systems, no PC is required for parameter setting.
Different zones can be defined so that the driver is only warned when it is really necessary. This means that the O3M can be used to its full potential depending on the situation, which helps to reliably prevent accidents. At the same time, false alarms are virtually impossible due to the patented PMD time-of-flight technology.
For special requirements, expert settings are available during set-up. Pre-programmed inputs and outputs are available for an additional signal light, buzzers, standby operation or the ready status of the system.
The 3D sensors are suitable for robust applications in indoor and outdoor areas. A high protecting rating and shock and vibration resistance as well as a wide temperature range meet all requirements for use in mobile machines.
Conclusion
Florian Rolf's summary: "The system is very good at minimising risk. I can use it on forklift trucks to prevent employees from entering the danger zone and to prevent a dangerous situation or risk situation from occurring in the first place." This means that the anti-collision system, which can be integrated very easily into existing vehicles, provides maximum safety for all types of mobile machines and supports the daily work of the drivers.

To set up the system, the user only needs to measure the height and inclination angle of the camera as well as the vehicle width and enter them in the controller.

Via extended parameter setting, different warning zones can be defined which will trigger certain output signals.