Baier & Schneider GmbH & Co.KG – More performance and transparency thanks to SAP add-on
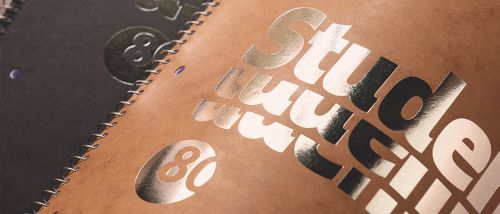
Transparency is one of the most crucial success factors for an efficient supply chain. In particular, this requires consistent data and coordinated production and delivery processes in supply chains across plants and locations. As the standard SAP system alone no longer satisfied the requirements of a centralized supply chain for the entire company group, a global manufacturer of paper products decided to implement an SAP add-on for the optimization of SAP-controlled logistics processes. Thanks to the GIB Suite, the company has since enjoyed optimized inventories and purchase order quantities, while also enjoying a reduction in operational processing times of up to 67%. In addition, greater transparency has meant that individual areas can be controlled centrally, thus ensuring an optimum strategic direction for the company group as a whole.
Goal: Improved production planning and transparent overview of supply chain
Baier & Schneider distributes the 20,000 items from its product range of all company brands – the best-known of which is “Brunnen” – to more than 16,000 business partners in over 40 countries from one logistics center. Highly functional technologies are crucial to ensuring an efficient flow of processes.
“As the standard SAP system alone had long since ceased to fulfill our requirements of an increasingly centralized supply chain for our company group, we looked around for a new solution,” reports Peter Nickel, Head of IT & Organization at Baier & Schneider GmbH & Co. KG. GIB came to the attention of the provider of paper products after a market analysis of software suppliers was conducted on the topic of supply chain optimization. GIB mbH from Siegen has become a specialist in the optimization of logistics processes in SAP. The GIB Suite represents the centerpiece of the IT company.
The target requirements were:
- improved production planning
- transparent overview of the supply chain status
- inventory optimization
- MRP master data optimization
- system-supported S&D planning
- integrated reporting on the supply chain
- ergonomic handling
- good reputation and project expertise of the provider
Roll-out and handling
The end of 2016 saw the implementation of the GIB Suite modules for controlling and operations, with the planning module introduced in 2017; Baier & Schneider is currently implementing the forecast module. The solution was first implemented in the main plant in Heilbronn and was then rolled out in the plant in Teichröda; only the planning module is used centrally in Heilbronn. The modules for controlling and operations went live about three months after the initial project start; the company managed to go live with the planning module after only one and a half days. In total, 40 to 50 users work with the GIB Suite modules.
Employee feedback on the modules has been positive overall. The highlight in the operations module, the tool used by MRP controllers in their daily business, is the “death zone” of purchasing, reports Kozan. This is a special display variant, which shows the procurement elements highlighted in color in relation to the replenishment lead time (RLT). Open procurement elements within the RLT are in this “death zone”. This view allows MRP controllers to keep track of procurement before the RLT.
“The solution has become an integral part of operations,” says Nickel, with Kozan adding: “Even though GIB consultants gave us some in-house training and train-the-trainer sessions were held by key users, operation in the standard SAP environment didn’t require a great deal of getting used to,” explains Kozan. “Dealing with the number of buttons in the modules was at times a little tricky to begin with.” If support is required from GIB, they are quick to process tickets and change requests on time and in the desired quality. “GIB is one of the most highly respected suppliers within the IT department,” according to Nickel.
Benefits in terms of productivity and utilization
The implementation of the GIB Suite modules has resulted in benefits impacting positively not least on concrete performance indicators. Kozan sums things up: “In the short term, we see the success of the SAP add-on in reduced operational processing times, in the medium term, in increased productivity and utilization of key aggregates, and in the long term, in optimized inventories and greater delivery capability.” “We’ve been able to reduce operational processing times by up to 67% in the planning of standard articles in purchasing.” The company was honored for this success with the SCM Award in 2017.
Conclusion
In summary, thanks to the transparency provided by the GIB Suite, the manufacturer of paper products has been able to sustainably optimize its inventories, including slow-moving items, and purchase order quantities using the tool’s modules. In particular, this transparency – as formulated in the target requirements – enables individual areas to be controlled centrally, across plants, and thus provides support in creating a strategically optimum direction for the company group as a whole.