- Supply Chain Management
- Sales & Operations Planning
- Inventory Management
Supply Chain Excellence (SCX) for Inventory Management
Enhance inventory planning and stock analysis in SAP with advanced inventory management tools
Key features
ABC/XYZ analysis
Classify items based on value and demand variability to manage fluctuating demand more effectively. Easily identify items requiring different management strategies.
Simulation and analysis tools
Simulate various supply chain scenarios to assess the impact of different decisions and identify potential risks. Consider factors like lead times, demand variability, and disruptions.
Key figures
Analyze detailed data on stock, consumption, issues, and receipts, categorized into values like last, highest, average, lowest, and typical, for a detailed view of supply chain performance.
Material segmentation
Manage inventory by grouping materials with similar attributes and applying tailored optimization strategies based on custom characteristics.
Replenishment Lead Time (RLT) Monitor
Manage and optimize the replenishment process using detailed insights into the lead times associated with inventory replenishment.
Range of Coverage (RoC)
Analyze the coverage of stock and requirements over specified periods to identify areas where stock levels are either too low or too high.
ABC/XYZ analysis: An inventory management strategy that addresses both value and demand variability

Focus efforts on the most critical inventory items
- AX items: High-value items with predictable demand — Focus on accurate forecasting and tight inventory control to minimize holding costs.
- AY items: High-value items with variable demand — Implement regular monitoring and adjust safety stock levels to ensure availability without overstocking.
- AZ items: High-value items with unpredictable demand — Maintain higher safety stock and flexibility in supply chain processes to handle demand variability.
- BX, BY, BZ items: Medium-value items across different demand variability levels — Balance control efforts and safety stock levels according to demand patterns and value impact.
- CX, CY, CZ items: Low-value items with varying demand patterns — Simplify control mechanisms while ensuring sufficient stock levels to prevent stockouts.
ABC/XYZ use cases
Inventory optimization
Allocate resources and management efforts based on the classification of items.
Demand forecasting
Adjust forecasting techniques and safety stock levels based on demand variability.
Cost management
Implement different control strategies for high-value and low-value items.
Multi-level simulation: A comprehensive tool for supply chain scenario analysis
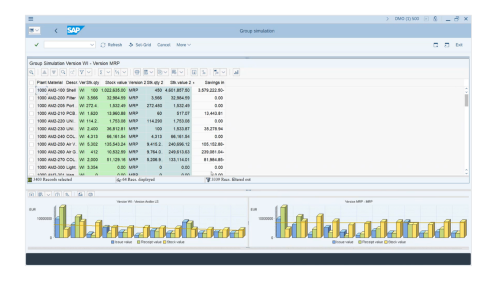
Prepare for and mitigate risks, optimize processes, and make informed strategic decisions
- Evaluate the outcomes of different hypothetical situations like changes in demand, supply disruptions, or new product introductions.
- Test the impact of altering key parameters like lead times, safety stock levels, order quantities, and production schedules.
- Optimize inventory levels by simulating different stocking strategies and their effects on service levels and carrying costs.
- Improve production efficiency by analyzing various scheduling scenarios and their impact on capacity utilization and throughput.
Simulation and scenario analysis use cases
Demand fluctuation management
Model different inventory and production strategies to identify an optimial strategy that balances service levels with inventory costs.
Supplier reliability
Assess the impact of delayed shipments and test alternative supplier options or increased safety stock to mitigate the risk of supplier failures.
New product introduction
Analyze the effects on existing production schedules, capacity, and inventory requirements to ensure a product launch with minimal distruptions.
Key figures: Essential metrics for evaluating and optimizing supply chain performance

Achieve greater efficiency, cost savings, and overall improvement in supply chain operations
- Track inventory levels, consumption patterns, and material flows to ensure operational efficiency.
- Analyze stock levels and consumption rates to optimize inventory holding and reduce carrying costs.
- Use average consumption and Range of Coverage (RoC) metrics to forecast future demand accurately.
- Monitor lead times and issue frequencies to identify potential bottlenecks and vulnerabilities in the supply chain.
- Track the value of inventory, issues, and receipts to manage and control supply chain costs effectively.
Stock key figures
- Stock value: Measure the value of inventory over time.
- Average stock: Analyze the typical amount of stock held over a specific period.
- Maximum and minimum stock: Identify stock level extremes with the highest and lowest stock levels recorded.
Consumption key figures
- Consumption value: Understand usage patterns and cost implications by tracking the value of goods consumed.
- Average consumption: Analyze the average rate of consumption.
Issue key figures
- Issue value: Analyze inventory turnover and useage based on the value of goods issued from inventory.
- Frequency of issues: Identify patterns and optimize inventory levels by measuring how often goods are issued.
Receipt key figures
- Receipt value: Support procurement and replenishment strategies by measuring the value of goods received into inventory.
- Number of receipts: Gain insight into supply chain efficiency by analyzing the frequency of goods receipts.
Range of Coverage (RoC) metrics
Material segmentation: Classify and manage inventory more effectively
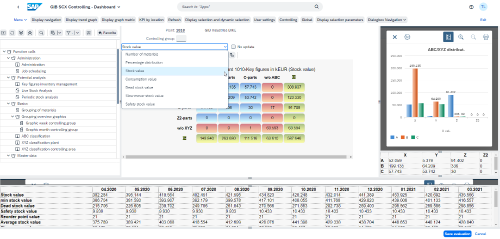
Optimize stock levels, procurement strategies, and overall supply chain efficiency by grouping materials based on specific characteristics
- Define up to three custom characteristics for material classification.
- Group materials based on attributes like usage rate, lead time, value, and demand patterns.
- Segmentation data is combined with key figures and other analytical tools to provide deeper insights.
- Updates are dynamic as material characteristics or business conditions change.
Material segmentation use cases
Inventory optimization
Group materials based on turnover rates and adjust inventory policies accordingly.
Procurement strategy
Classify materials based on supplier lead times and reliability to develop tailored procurement strategies.
Demand forecasting
Segment materials by demand patterns to apply appropriate forecasting models.
Production planning
Categorize materials by their role in the production process (e.g., raw materials, work-in-progress, finished goods).
Replenishment Lead Time (RLT) Monitor: Track and analyze the time it takes to replenish inventory

Meet demand without incurring excess holding costs or stockouts
- Monitor the actual time taken for each replenishment cycle.
- Analyze historical lead time data to identify trends and variances.
- Set thresholds for acceptable lead times and triggers alerts when these thresholds are exceeded.
- Assess supplier performance by comparing actual lead times against agreed standards.
RLT Monitor use cases
Stock level maintenance
Maintain optimal stock levels by ensuring timely replenishments.
Safety stock calculation
Calculate appropriate safety stock levels based on lead time variability.
Supplier evaluation
Evaluate supplier reliability and performance based on lead time consistency.
Negotation tool
Negotiate better terms with suppliers by highlighting areas of improvement.
Range of Coverage (RoC): Evaluate and manage inventory levels against forecasted requirements
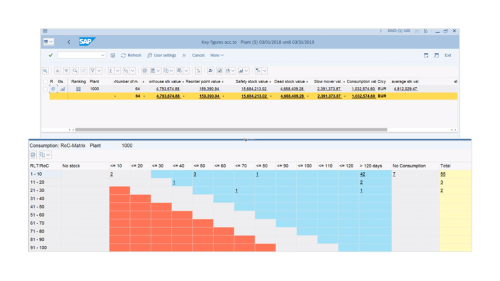
Maintain optimal inventory levels by identifying potential stock issues
- Assess how long current inventory will last based on average consumption rates.
- Evaluate whether inventory levels are sufficient to meet future demand over a given period.
- Generate alerts for potential stockouts or overstock situations.
- Drill down into specific items or periods to investigate the root causes of coverage issues.
RoC uses cases
Inventory optimization
- Adjust stock levels, reduce carrying costs, and avoid stockouts.
- Determine appropriate safety stock levels based on variability in demand and lead times.
Demand Planning
- Enhance the accuracy of demand forecasts by continuously comparing them with actual inventory usage.
- Identify seasonal variations in demand for better planning and inventory adjustments.
Supply chain resilience
- Identify potential risks in the supply chain due to insufficient coverage and take corrective action.
- Facilitate better coordination with suppliers with visibility into future inventory requirements.
Frequently asked questions
Schedule your live demo today
Discover how SCX for Inventory Management can optimize your inventory strategies within SAP. Schedule a personalized demo with our expert team to explore our solution's full capabilities and see how it can benefit your business.
- See SCX for Inventory Management in action: Get a comprehensive walkthrough of our key features and functionalities tailored to your specific needs.
- Ask the experts: Have your questions answered by our knowledgeable team and learn how SCX for Inventory Management can address your unique challenges.
- Tailored recommendations: Receive personalized insights and recommendations based on your business requirements and goals.
Contact us to schedule your demo
- Email: usa@ifm.com
- Schedule online: Submit the form below