- Supply Chain Management
- SAP-based software
- New Release 25.0
- Shop Floor Integration
Highlight Features in Shop Floor Integration (SFI)

Transparent, reliable, labour-saving: finally track & trace in intralogistics
The new release includes numerous new automation functions for your SAP processes. From now on, e-Kanban, automated incoming and outgoing goods and production confirmations are also possible.
The new track & trace initialisation app for handheld and PC can be used on mobile and stationary devices. This allows SAP business data to be manually assigned to tags* very quickly. Tags can even be initialised automatically in static processes. The API interface for third-party systems also makes it easy to transfer tag assignments from platforms such as moneo or Localino. Automatic and therefore seamless logging of all activities is of course also included.
Another key component of the new track & trace is the visualisation of object positions. This makes it possible to determine and display the exact storage location or the current transport position of materials, containers, production resources or production orders at any time.
*Tag = Labelling
The right track & trace solution for your infrastructure
Whether you work with QR codes, barcodes, RFID or even RTLS systems, we can provide you with the right solution – because the ifm solution Shop Floor Integration works independently of technology.
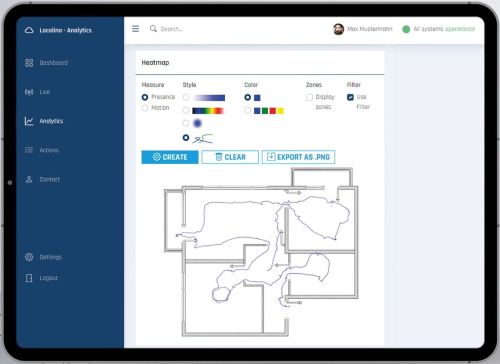
Shop Floor Integration with Localino
This RTLS-based high-end solution offers ground-breaking possibilities in the tracking of materials, production aids and other tag-capable products. Modern RTLS tags enable localisation via antennas. This means that the system is not tied to fixed transport routes and can even be used outdoors.
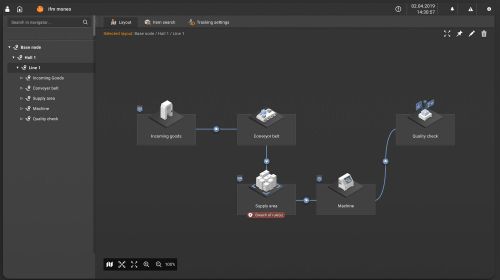
Shop Floor Integration with moneo
moneo is based on fixed reading units for detecting optical or electronic tags (RFID). These tags are often inexpensive and therefore suitable for bulk goods and one-way processes. Using the moneo platform, the various types of tags can be easily integrated into the SFI Track & Trace system. This technology is easy to use for clearly defined transport routes.
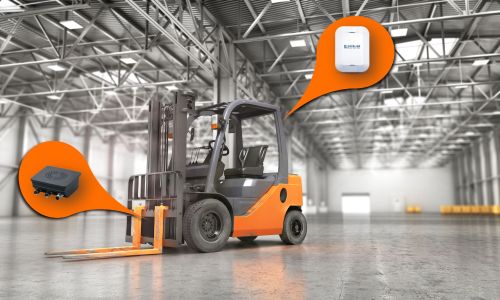
Hybrid solution is all the rage
To be able to implement localisation throughout the plant and still keep an eye on and control costs, we at ifm also offer a hybrid track & trace solution.
The systems are combined: RTLS tags are then installed on forklift trucks, for example, which can then be localised without restriction in the open area. The pallets and containers, on the other hand, are labelled with a low-cost RFID tag. These tags could then be read by a sensor attached to the stacking fork. With this small workaround, you always know exactly where your forklift truck is and, as a result, where the transported pallet or container is located.
In SFI Track & Trace, the RTLS and RFID signals are processed and stored as combined data. This also enables an expost view of the transport routes, transport times, lay times and intermediate stations.
Localino e-paper tags – small information wonders!
Flexible helpers in intralogistics can be so-called e-paper tags. These are small displays that serve both as a localisable tag and also offer a dynamic display of texts and symbols.
E-papers are therefore a two-in-one solution and offer advantages if, for example, the result of a quality inspection is to be transferred to a container that is stored at a different location.
SFI is able to transfer SAP information to these e-paper tags or to be supplied with location information about the object by them.
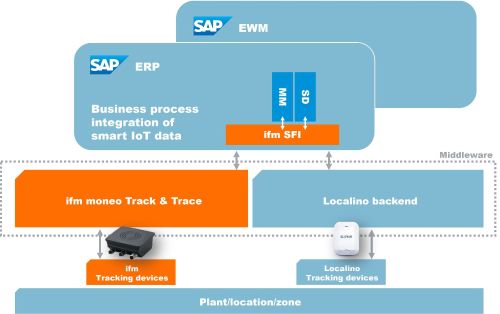
More productivity, less frictional losses
Processes help to create transparency and give everyone involved the certainty that they are doing the right thing and acting within the scope of their authorisations and responsibilities. Processes should therefore be documented, practised and monitored.
Nevertheless, many processes today depend on people entering the right data at the right time. To reduce this error factor, many data entries in intralogistics processes can be automated using track & trace.
The e-Kanban, goods receipt, goods issue and production feedback processes are briefly described below:
e-Kanban process

Goods receipt process

Goods issue process

Production feedback process
