- Supply Chain Management
- Resource Center
- New Releases
- Inventory Management
Release 25.0: New Inventory Management features

Enhanced tools for smarter inventory management and analysis
Release 25.0 brings numerous new tools and features to help you achieve greater control, efficiency, and accuracy in your inventory management processes. From new Fiori apps for deeper insights to enhanced automation and performance optimizations within SAP S/4HANA, this release is designed to support your business in making smarter, data-driven decisions.
Fiori Apps
New, user-friendly interfaces for analyzing trends, slow-moving items, ABC/XYZ classifications, and more.
Replenishment Lead Time (RLT)
TREE mode for better visualization of BOM explosions and lead time calculations.
Target Workbench (TWB) & Rule Workbench (RWB)
Enhanced dynamic graphics, automated issue assignment, and simplified rule management.
SAP S/4HANA
Performance boosts with runtime optimizations and alternative consumption calculations.
New Fiori apps for advanced inventory analysis
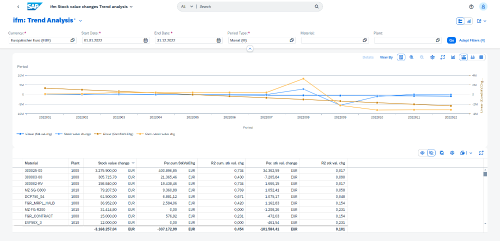
The new Trend Analysis app provides a comprehensive view of how your stock values have changed over time, helping you identify trends, inventory drivers, and areas for optimization.
Insights provided by the app:
- Stock development over time: Monitor how your inventory levels have changed during a specific period.
- Growth or decline analysis: Identify whether stock levels are increasing or decreasing and by how much.
- Average change per period: See the average value increase or decrease of your inventory over defined time frames.
- Inventory drivers and reducers: Pinpoint which materials contribute the most to inventory growth or reduction.
- Trend analysis: Understand the speed and direction of inventory changes — whether stock levels are rising or falling quickly or gradually.
This app provides a clear picture of your stock trends, enabling you to make strategic, data-driven decisions that enhance inventory management and operational efficiency.
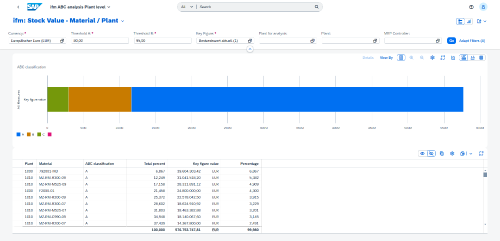
The new ABC Analysis app offers a modernized approach to analyzing your materials and their value, providing deeper insights that go beyond traditional ABC analysis.
Insights provided by the app:
- Identify high-value materials: Determine which materials contribute the most to your plant’s overall inventory value.
- Multi-plant analysis: Assess ABC classifications across multiple plants simultaneously for a holistic view of your inventory.
- Targeted material evaluation: Perform ABC analysis for specific areas of responsibility, focusing on the materials that matter most to your operations.
- Stock distribution insights: Visualize how stock values are distributed across different product types within your inventory.
- Flexible classification metrics: Analyze how ABC classifications change when applying different metrics or time periods, allowing for tailored assessments based on your business needs.
With this app, you gain clear, actionable insights for better inventory management and more accurate material planning, making it easier to optimize stock levels and improve operational efficiency.
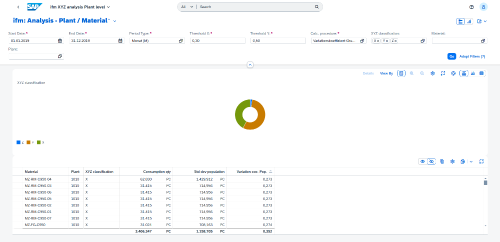
The new XYZ Analysis app helps you classify materials based on demand variability, giving you the information needed to improve inventory planning and procurement.
Insights provided by the app:
- Flexible selection: Choose which materials to analyze and set the time period for your review.
- Demand classification: See how materials are categorized, ranging from stable demand to highly variable demand.
- Optimized planning: Identify demand patterns and fluctuations to adjust your inventory and procurement strategies accordingly.
This app makes it easier to understand and manage demand variability, helping you plan inventory more efficiently and respond quickly to changing needs.
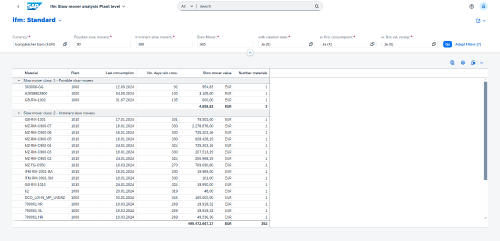
The new Slow-Moving Item Analysis app helps you not only manage existing slow-moving stock but also identify materials at risk of becoming slow-moving, allowing for proactive planning and action.
Insights provided by the app:
- Early identification: Spot materials that may become slow-moving items in the future and take action before they affect your inventory performance.
- Forward-looking analysis: Assess which materials are likely to slow down in movement over time and plan accordingly to prevent excess stock.
- Detailed tracking: Monitor current slow-moving items and their values across categories like product group, product type, and division.
This app provides a forward-looking view of your inventory, helping you prevent stock issues before they arise and maintain efficient, cost-effective stock levels.

The new Stock Value World Map app expands your view from global to regional, allowing you to track inventory levels within specific regions of a country for better stock management and planning.
Insights provided by the app:
- Detailed regional view: Zoom in from a country-level view to see stock values at the regional level for more granular tracking.
- Bottleneck detection: Identify potential stock shortages or surpluses in specific regions and take action quickly.
- Improved planning: Plan short-term stock movements more efficiently by understanding inventory distribution across regions.
This feature gives you a clearer view of where your inventory is located, making it easier to optimize stock levels and respond faster to regional demands.

The enhanced Stock Value World Map app displays the flow of incoming and outgoing goods between countries and regions, giving you a clear view of your supply chain's financial movements.
Insights provided by the app:
- Track financial flows: See where money is moving across your supply chain, from suppliers to distribution regions.
- Identify key hubs: Pinpoint the most active economic regions in your supply chain to prioritize and optimize operations.
- Optimize supply chain costs: Use the visualized data to find areas where costs can be reduced or processes improved.
This feature enhances supply chain transparency, helping you make informed decisions to streamline operations and manage costs more effectively.
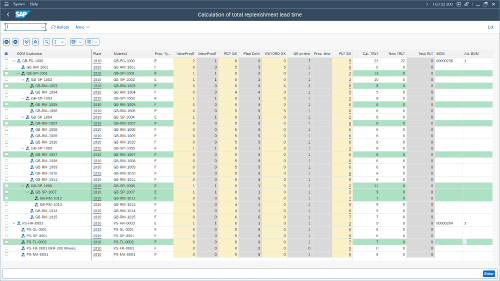
The new TREE mode for BOM explosion provides a structured view of your Bill of Materials (BOM), making it easier to manage and understand the total replenishment lead time (TRLT) for your materials.
Insights provided by the app:
- Clear BOM visualization: View BOM components in a hierarchical tree structure, making complex material relationships easier to navigate.
- Critical path management: Identify and manage the critical path in your supply chain, ensuring materials arrive on time.
- Flexible time conversions: Convert TRLT calculations into either working days or calendar days for more accurate and adaptable planning.
This new mode gives you better visibility into lead times, helping you plan more accurately and avoid delays in your supply chain.
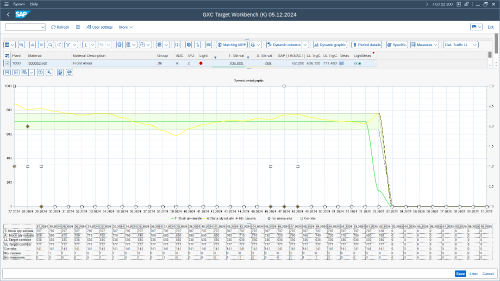
The updated Target Workbench dynamic graphic provides a clear and detailed view of your target vs. actual performance, making it easier to track progress and assess the effectiveness of your actions.
Insights provided by the app:
- Clear target vs. actual comparison: Visualize your performance against targets, with an added corridor display to highlight acceptable ranges.
- Performance tracking over time: See when causes and corrective measures were recorded, allowing for better evaluation of their impact.
- Flexible viewing options: Customize your display to show data by weeks or months and choose the number of periods to view, ensuring the data fits your specific needs.
This enhanced visualization helps you monitor performance more effectively, quickly assess the success of your measures, and make informed decisions to improve your supply chain operations.
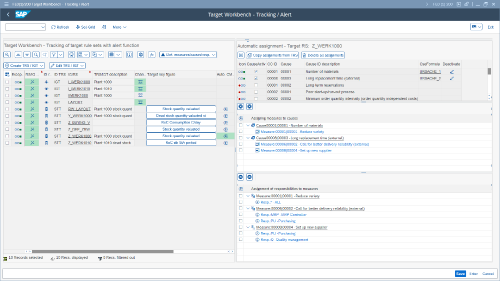
The new automation feature in Target Workbench (TWB) allows you to automatically assign causes, corrective measures, and responsibilities, saving time and ensuring consistency in issue management.
What this automation offers:
- Automated assignments: Causes, measures, and responsibilities are assigned based on predefined formulas within the TWB data structure, reducing manual effort.
- Full control in TWB monitor: View, adjust, delete, or expand automated assignments at any time to ensure accuracy and relevance.
- Faster issue resolution: Enables early identification of issues and quick implementation of corrective actions, ensuring smoother supply chain operations.
This automation streamlines your workflow, improves response times, and ensures that responsibilities are clearly defined and tracked throughout the issue resolution process.
Simplified Rule Workbench
The new simplified mode in Rule Workbench (RWB) improves usability by providing a clearer, more focused view while enhancing system performance for data collection in SAP S/4HANA.
What the new RWB mode offers:
- Streamlined interface: Reduces visual clutter, making it easier to focus on essential tasks without unnecessary distractions.
- Faster data collection: Significantly improves data retrieval speed, especially when working with large volumes of special stock.
- Optimized SAP integration: Delivers relevant information more quickly and efficiently, minimizing system load and improving resource management.
This new mode enhances user experience, speeds up operations, and ensures that your inventory data is collected and processed efficiently.
SAP S/4HANA runtime optimization
The latest runtime optimization in SAP S/4HANA improves the speed and efficiency of data collection for special stocks, ensuring faster access to critical inventory insights.
What this optimization delivers:
- Accelerated data processing: Enables quicker and more targeted retrieval of key figures, especially in environments with high volumes of special stocks.
- Optimized system performance: Reduces system load by improving how data is collected and processed.
- Shorter loading times: Ensures faster availability of relevant information, improving responsiveness in inventory management.
These enhancements allow for more efficient resource usage, helping businesses maintain smooth operations without performance bottlenecks.
Alternative consumption calcuation in SAP S/4HANA
The new alternative consumption calculation feature in SAP S/4HANA gives businesses more control over how they analyze inventory consumption by offering the option to use SAP standard consumption calculations or a more customized approach.
What this update offers:
- Standardized data for comparability: Use SAP’s standard consumption calculation as a baseline to ensure consistency across key figures and analyses.
- Customizable consumption models: In cases like stock optimization, businesses can adjust calculations to better reflect their specific needs.
- Future flexibility: Upcoming enhancements will allow full customization, enabling users to choose between SAP’s standard method, a tailored company-specific approach, or an independent interpretation.
This improvement ensures that businesses can maintain consistency where needed while having the flexibility to refine calculations for more accurate and relevant insights.