- Supply Chain Management
- Resource Center
- New Releases
- Shop Floor Integration
Release 25.0: New Shop Floor Integration (SFI) features

Automate SAP processes for greater transparency and efficiency
Release 25.0 introduces new automation features for Track & Trace in intralogistics, helping businesses reduce manual effort, improve process reliability, and enhance real-time visibility across shop floor operations. Whether you’re managing e-Kanban, goods receipt, production confirmations, or outbound logistics, these updates streamline SAP processes while integrating seamlessly with RFID, QR codes, barcodes, and real-time localization systems (RTLS).
Track & Trace Initialization app
With Release 25.0, the new Track & Trace Initialization App enables businesses to quickly assign SAP business data to tags using handheld or stationary devices.
What this app offers:
- Manual & automated tag assignment: Assign business data to tags (RFID, QR codes, barcodes, RTLS) instantly — either manually or via automated initialization.
- API integration with third-party systems: Seamlessly transfer tag data from platforms like moneo or Localino.
- Automated tracking & logging: All activities are recorded automatically, ensuring full traceability.
- Visual position tracking: Display the exact location of materials, containers, production tools, and orders in real time.
By eliminating manual tracking errors, these enhancements improve inventory accuracy, logistics planning, and overall process efficiency.
Choosing the right Track & Trace solution for your infrastructure
Shop Floor Integration is designed to work with any tracking technology, ensuring flexibility across QR codes, barcodes, RFID, and RTLS systems.
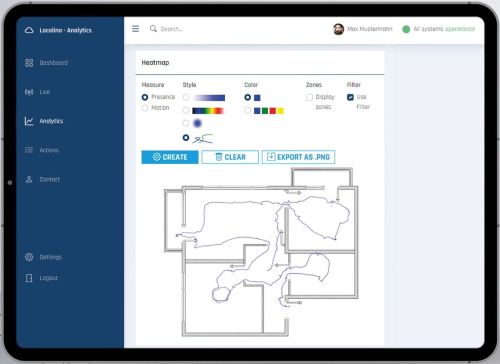
RTLS-based tracking with Localino
The Localino RTLS platform is a real-time localization system that offers advanced tracking for materials, production tools, and tag-enabled assets.
- Precision tracking via antennas: Not restricted to fixed transport routes, allowing free movement indoors and outdoors.
- Real-time location updates: Provides immediate visibility into the location of materials and equipment.
- Seamless SAP integration: Automatically updates SAP records without manual intervention.
This solution is ideal for dynamic production and logistics environments that require continuous monitoring of moving assets.
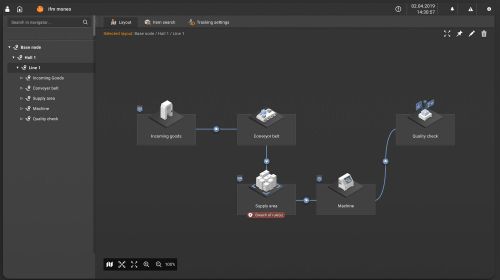
RFID & optical tag tracking with moneo
The moneo platform is designed for fixed-location tracking, making it a cost-effective solution for bulk goods, one-way processes, and structured transport routes.
- Reliable RFID tag scanning: Uses stationary reading units to detect RFID or optical tags.
- Scalable for high-volume operations: Ideal for automated goods receipt, inventory tracking, and logistics verification.
- Easy integration into SAP: Ensures that tagged items are automatically updated in SAP S/4HANA.
This system is well-suited for warehouses, conveyor-based transport, and structured material flows where items follow predictable paths.
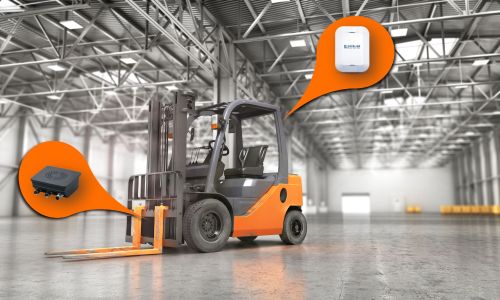
Hybrid Track & Trace
For businesses that need full-plant localization without excessive costs, ifm offers a hybrid Track & Trace solution that combines RTLS and RFID.
How it works:
- RTLS tags on forklift trucks enable unrestricted movement indoors and outdoors.
- RFID tags on pallets and containers allow for cost-effective inventory tracking.
- Forklift-mounted RFID readers scan and update SAP with each pickup and drop-off.
By combining these technologies, businesses can maximize tracking accuracy while controlling costs, ensuring efficient logistics and shop floor transparency.
Localino e-paper tags: Real-time tracking with dynamic data
E-paper tags are fleixlbe, digital displays that serve dual functions:
- Act as a localizable tag for tracking materials, containers, and production resources.
- Automatically receive and display SAP information, such as quality status, production details, or order instructions.
These tags help businesses reduce manual SAP postings, improve process visibility, and eliminate time-consuming searches by dynamically updating key operational data.
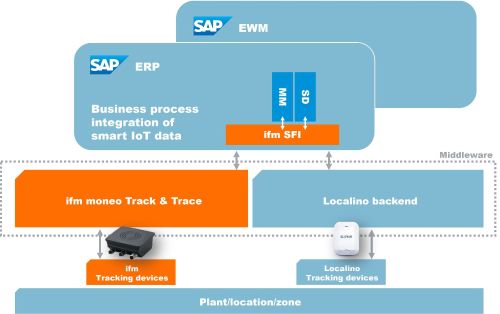
How it works:
- Install reader units: Reader units are placed in critical tracking areas within the plant, site, or zone.
- Tag the objects: Materials, containers, production tools, and equipment are fitted with RFID, QR code, barcode, or RTLS tags.
- Detect & record movement: As objects move, the reader units capture location data and send it to the SFI platform for processing.
- Process & integrate with SAP: The system dynamically assigns the tracked information to the corresponding SAP process, ensuring real-time updates and accurate inventory records.
Increase productivity and minimize errors with automated Track & Trace
Efficient shop floor and intralogistics processes rely on transparency, accuracy, and automation. However, manual data entry introduces delays and errors, creating inefficiencies that impact productivity.
With Track & Trace, businesses can automate key intralogistics workflows, ensuring real-time updates in SAP, eliminating manual input errors, and improving process reliability.
e-Kanban process

Automate material replenishment
SFI and Track & Trace automate e-Kanban workflows, ensuring a seamless, demand-driven material supply without the need for manual SAP postings.
How it works:
- Each Kanban box is equipped with an RFID tag linked to its unique Kanban ID.
- As the tagged box passes through a registration station, its status is automatically updated in SAP.
- The system triggers downstream provisioning processes, ensuring materials are replenished as needed.
Automated goods receipt process

Faster, more accurate inbound logistics
With SFI and Track & Trace, the goods receipt process is fully automated, ensuring real-time updates in SAP, eliminating manual effort, and improving inventory accuracy.
How it works:
- RFID tagging at supplier level: The supplier packs goods and attaches an RFID tag to the container (pallet, bin, etc.).
- Order data assignment: The supplier links order details (order number, item, quantity, etc.) to the tag via a cloud-based application.
- Automated SAP posting: When the container passes a registration station, the SAP goods receipt is instantly processed—no manual input required.
- Ongoing tracking: If the container is moved or stored, the tag remains active, providing continuous status updates.
- Closed-loop container management: If the business operates a closed-loop system, tags remain on containers permanently, requiring only supplier data updates for each shipment.
Automated goods issue process

Faster, more reliable outbound logistics
With SFI and Track & Trace, the goods issue process is fully automated, ensuring real-time shipment tracking, accurate order fulfillment, and seamless SAP updates — without manual intervention.
How it works:
- Tagging of outbound goods: Containers or pallets are fitted with RFID tags containing essential shipment details, such as delivery number, position, and quantity.
- Automated goods issue recording: When the pallet or container passes through a recording station, the system automatically scans and validates the shipment.
- SAP goods issue posting: The goods issue is instantly updated in SAP, eliminating the need for manual entry.
- Automated shipment verification: The system can also validate loaded goods to ensure the correct products are placed on the right truck, reducing mis-shipments.
Automated production feedback

Real-time tracking & process visibility
With SFI and Track & Trace, the production feedback process is fully automated, ensuring real-time tracking of work-in-progress (WIP), accurate production reporting, and seamless SAP updates without manual intervention.
How it works:
- RFID tag assignment: Before production begins, each container or clipboard is fitted with an RFID tag linked to the production order and container ID. Additional details like material, batch, and planned quantities can also be assigned.
- Work center arrival & process start: The container is moved to the first production work center, and production begins.
- Real-time quantity adjustments: If production output deviates from the planned quantity (e.g., due to rejects), workers can adjust recorded quantities via a mobile app.
- Automated tracking across work centers: As containers move to the next production stage, recording devices detect their arrival, and feedback is automatically logged for the previous operation.